
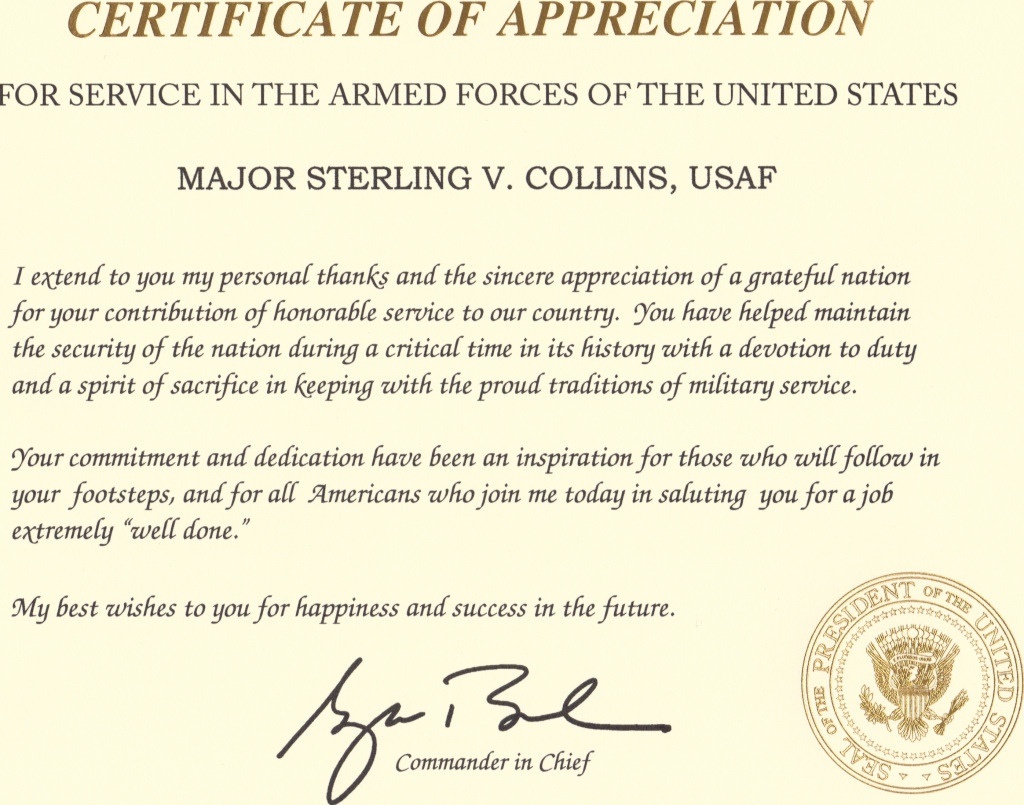
- #Einstein platform services certificate retired how to
- #Einstein platform services certificate retired software
- #Einstein platform services certificate retired series
“The trend went from using DFA in simplifying the design and shifted to DFM to challenge suppliers on the cost of piece parts,” he said. Of late, Dewhurst has seen a shift in emphasis. They can be provided as default values in a general analysis or tuned to and edited by an individual manufacturer. They include factors such as machine rates, operator rates, material costs, and scrap value.
#Einstein platform services certificate retired software
“We assign accurate and credible costs to those parts,” he said, using software that calculates manufacturing cycle time through embedded equations developed by the company over the last 30 years.
#Einstein platform services certificate retired series
“Our DFM methodology contains a series of about 30 manufacturing cost models to look at those design decisions.” A design team now using integrated DFMA (Design for Manufacturing and Assembly) can potentially look at three, four, or five different but appropriate methods of producing parts. “We needed to understand the impact on cost of these more complex, fewer parts resulting from DFA,” said Dewhurst.

#Einstein platform services certificate retired how to
Engineers typically think of how to make individual parts as inexpensively as possible without considering the total cost savings from reducing part count, even if individual parts cost more.įrom DFA grew Design for Manufacturing, or DFM, which turns back to thinking about cost and manufacturability of the part-like my problem with the submarine bearing. “Thinking about cost control in this sense can be a ‘lightbulb’ moment,” he said. Fewer parts mean both a less complex end product and fewer parts flowing through the plant and supply chain. “What ultimately controls the cost of a product is part count,” Dewhurst said. He is the son of one of the company founders. “DFA is all about producing elegant designs with as few parts as possible that still satisfy customers,” explained Nick Dewhurst executive vice president of Boothroyd Dewhurst. (Wakefield, RI), a pioneer in the field, was founded by two university professors who had been developing solutions for a related problem, Design for Assembly, or DFA. In the mid-1980s, the industry was understanding that many designs were not only difficult to make, like my bearing, but debilitatingly complex. That was my introduction to the need for Design for Manufacturing.

Not only had the plant manufacturing engineer seen the concept before, he pointed out-one more time-the many reasons you could never, ever build such a thing. “Go see what the plant makes of this,” he said. There was just one last step my supervisor insisted on before he would let me start detailed design. It would be lightweight, strong, and use a minimal amount of material.
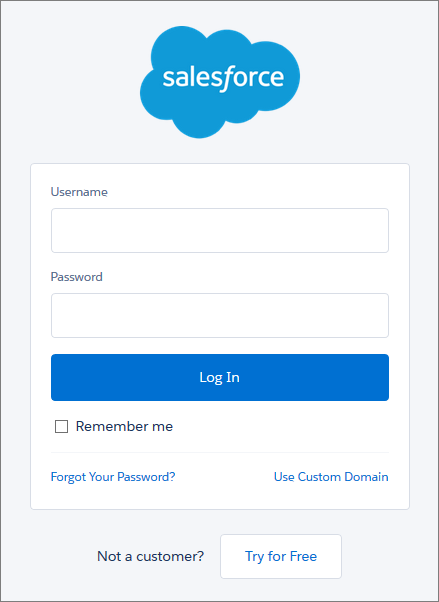
Recommended cutting speeds and paths are automatically taken from the DFM library and applied to the hardness of the stock stainless steel.Īs a beginning engineer, six months into my first job, I completed a rough design concept of what I thought was a novel way to build a bearing for a submarine propulsion shaft. Capturing and applying experience in a disciplined manner is vital, for both design engineers and their manufacturing counterparts DFM Concurrent Costing 3.0 software from Boothroyd Dewhurst, shown here calculating the optimum machining time and cost for a rough cylindrical turning operation for a stainless-steel part. Controlling cost and complexity starts in design.
